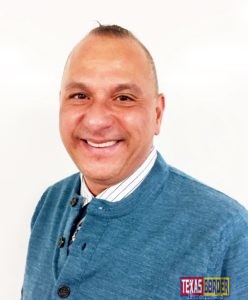
By Ricardo R. Olivares
Texas Border Business
Over the last few years there has been an emphasis to create safer and healthier worksites that meet greater safety requirements. The goal is to improve the safety, health, and well-being of the country’s workforce, especially here in the Rio Grande Valley and in cities along the Texas border.
We have an astounding number of warehousing, storage, distribution and transportation operations located from Brownsville all the way to Laredo. These same operations have begun a concerted effort to prevent accidents, injuries, and even fatalities resulting from work activities.
The logistics industry has increased their safety trainings and awareness, which has developed into an initiative to improve safety and health performance by reducing the injuries and time away from the workplace, identifying the worksites, focusing on hazards that may contribute to injuries and illnesses, and ultimately developing a plan to control or eliminate those hazards.
Some of the focused areas of concerns are:
- Contact with objects – hazards associated with unsafe operation of powered industrial trucks
- Overexertion – hazards associated with ergonomic issues, unsafe lifting activities
- Falls – same level falls and fall hazards to a lower level
- Overhead and gantry cranes
- Hazardous materials
- Many more identified hazards
There has been tremendous growth in the logistics industry. With Mexico considered by many to be the “third coast”, the Occupational Safety and Health Administration (OSHA) and the Bureau of Labor Statistics (BLS) have been reviewing local and national data to identify issues in the industry. They have found and identified many events or exposures that have become priority; industrial truck accidents, falls, overexertion involving ergonomic stressors, hazards primarily attributed to lifting, and transportation accidents.
Industrial truck and forklift accidents include employees being struck by forklifts, forklift tip overs, fall from platform on forklift, and crushed by forklift. Back injuries can be the immediate result of improper lifting techniques, lifting loads that are too heavy, and repetitive motions done incorrectly associated with the back. Transportation accidents occur because of numerous situations; inexperience, fatigue, not paying attention or being focused, texting, alcohol, drugs and many more.
As mentioned before, the logistics industry is aware and concerned with these safety issues and is working to reduce the number of injuries and illnesses resulting from the focused hazards. A system needs to be created early to identify and correct focused hazards which have resulted in or have the potential for serious injuries, illnesses, and fatalities. The goal is to reduce the number of serious hazards and offer continued safety and health trainings to all involved. Safety training is the key to success, implementation of the safety plans, and communication to employees.
Effective safety and health programs should include:
- Management and Leadership
- Employee participation
- Identification of Hazards through Worksite inspections
- Hazard prevention and control
- Employee and supervisory training
- Enforcement of the Safety Program
The roles and responsibilities of first line supervisors and team leaders have changed. They are still the direct link between management and the workforce. We still have to produce quality goods and services to customers, but employee safety should always be a priority. The supervisor must constantly watch over and inspect the workplace and keeping in mind the three E’s of safety: engineering, education, and enforcement.
As a result, today’s supervisor or team leader must become skilled in three aspects of loss control; learn to recognize hazards, learn the acceptable level of risk for department operations, and learn how to control hazards to prevent injuries, illnesses, and property damage. No safety program can eliminate all the risks and hazards from the job, but being aware and trained can help you come as close to this ideal as possible. The more you know about the hazards in your workplace and how to control them, the more everyone in the organization will benefit.
Ricardo R. Olivares, MS-HRM, MAA-OD. He is the Program Chair – Business Administration (Careers) President and Council of Chairs South Texas College.
References: OSHA.gov