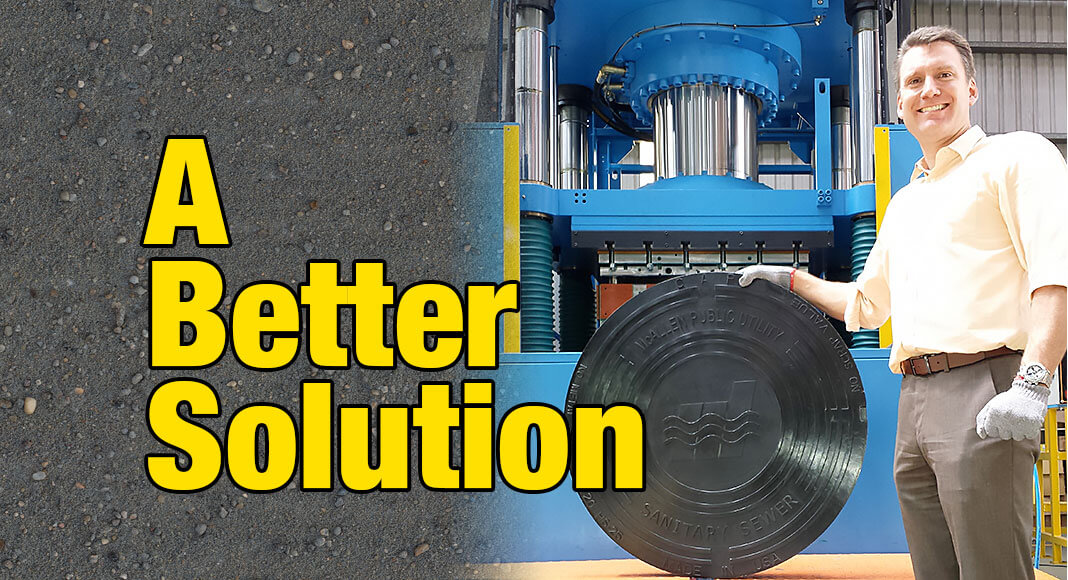
Special To Texas Border Business
Stormwater, floodwater, overflowing levees, and rising tidal waters, (etc.) are meant to be drained back into our natural waterways via storm systems. Groundwater known as Infiltration, and stormwater known as Inflow will also flow into our sanitary sewer system (Infiltration and Inflow or I&I) through gaps and holes.
Unlike the storm and drainage systems, the sanitary systems deliver fecal matter and other toxic chemicals to wastewater treatment plants. These sanitary systems have limited capacities, and when the I&I – not requiring treatment – enters the sanitary system the total volume can often exceed that capacity. The result of exceeding the sanitary sewer capacity is that the pathogen-filled sewer water reverses, surges, and spills into the streets, properties, rivers, lakes, and oceans. Sanitary Sewer Overflows or SSOs are a leading cause of water pollution amounting to 32 trillion gallons of pollution each year according to Nature Conservancy Magazine.
SSOs also cost cities millions each year from EPA fines, unnecessary rain guards, high wastewater treatment costs, electricity for added pump-time operation, and astronomic capital costs on over-capacity plants designed for high rainwater events. Reducing I&I allows for lower investment in smaller capacity treatment plants.
How does a composite manhole cover help prevent I&I?
Specifically, the compression molding composite process reduces the potential for part-to-part dimensional variation compared to iron casting allowing for a closely mated cover-frame fit. Plus, because composites are corrosion resistant, no oxide molecules develop in between the cover and frame allowing for tighter design tolerances.
For example, Fulton County, GA recently reported a 100% spillover elimination and 50% pump run time decreases on their first line by implementing composite manhole cover assemblies as part of a comprehensive solution. This eliminated millions of gallons of sewage that used to enter the Chattahoochee River with each major rainfall for the past 30-plus years.
In water utility vaults, the watertight package allows maintenance of water meters and valves without evacuating rainwater from the vault (“dewatering”). And as a bonus, wastewater crews report that being so precisely mated and sealed, the composite assembly greatly improves odor retention.
Municipalities have also suffered when opening traditional manhole covers stuck to the frames from debris and sometimes iron oxide particles.
Sewer gas (H2S) corrodes iron covers in many collection systems especially around lift stations, air release valves, and water treatment plants. The common solution is striking the cover with a sledgehammer to dislodge the cover from the frame. Time-consuming and frustrating, the pounding has caused operator injuries from back strains, eye contusions, and skin lacerations from bouncing debris caused by the hammer strike. Pounding manhole covers also damages the cover integrity, breaks the supporting frame, and simply results in skipped inspections if the operator cannot open it. In extreme cases, it is easier for municipalities to excavate the entire assembly than separate the cover and frame.
Composite manhole covers are inherently corrosion resistant so you can forget those expensive, toxic coatings used for iron that eventually peel off. Costly coatings – banned from states- applied to the covers are not necessary. Municipalities with extremely high H2S system concentrations are reporting that not even one assembly required a sledgehammer or special tool to open the unit – despite the presence of rocks and sand. These excellent results were achieved after four years, and thousands of assemblies used from one U.S. composite manufacturer.
Composite covers weigh approximately half or even one-third of traditional covers reducing operator disability, workman’s compensation liability, and ER costs resulting from back, finger, and toe injuries.
The composite assembly’s lighter weight and faster handling eliminates the need for heavy lifting equipment and work crews allowing contractors to devote more resources to laying pipe rather than setting manholes. They simply set the manhole, assign one operator to the install, and move the crew down the line.
Composite covers eliminate the root cause of manhole cover theft: money for metal that thieves sell to scrapyards. Fewer stolen covers mean reduced replacement costs, vehicle damage, and pedestrian falls. Thermosetting, UV-inhibited composite formulas give strength and weatherability. Composites are also transparent to transmission signals. There is no need for drilling antennae holes and attaching impact shields that can get damaged by vehicle impact. Some composite companies offer manhole covers in colors, stone-looks, custom logos, and with encapsulated RFIDs for asset management. Composite molding eliminates the toxic emissions and waste that some iron foundries produce. Composite assemblies are molded at 300°F or less, while iron requires energy for a 2700°F process. Finally, with a new compression molding process, composite assemblies are now becoming affordable and available in weeks not months.
CAP-
In 2015, W. Chad Nunnery founded Composite Access Products (CAP) to mold composite manhole cover assemblies and related products. CAP is the first U.S. compression molder of traffic-rated composite manhole covers. CAP has the only state DOT approval letter for U.S. composite manhole covers used “within the roadway”. CAP has installed assemblies in over 400 municipalities in 45 states within just four years since production started.
In October 2020, CAP was honored with the Award for Composites Excellence (ACE) from the American Composites Manufacturers Association (ACMA). Composite Access Products is located at 5216 N. 26th St. in McAllen, Texas 78504-4803. You can find CAP on the web at www.justcapthat.com, or call (956) 844-344-CAP1 (2271) for more information.